Technology
The Future of Warehouse Automation: Exploring Modern Storage Solutions and the Role of Drive-In Racks
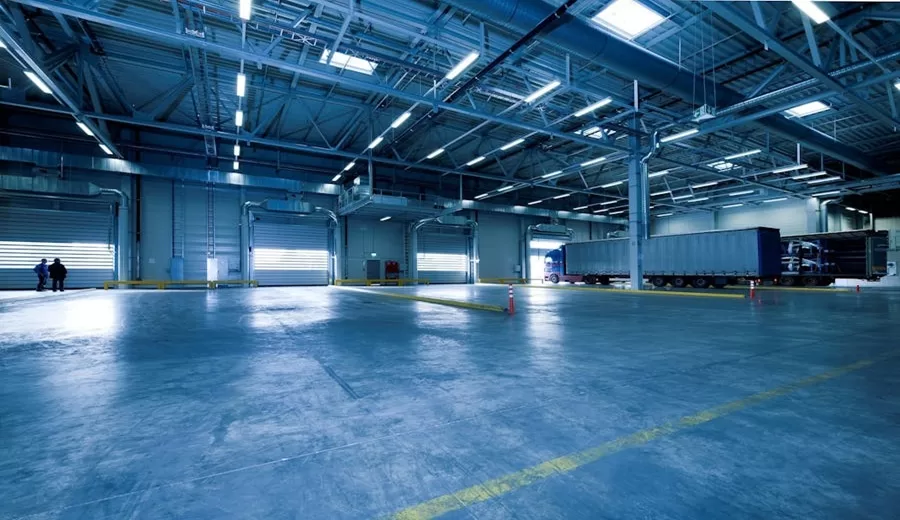
In the fast-evolving world of logistics and supply chain management, advancements in warehouse automation are transforming how businesses operate. From reducing labor costs to improving storage efficiency, modern automation technologies are reshaping the way industries handle their inventory.
At the heart of this transformation is the dynamic evolution of storage solutions, with technologies like drive-in racks playing a critical role in optimizing space and enhancing operational efficiency.
If you operate a warehouse, you need to understand the latest solutions to stay competitive. Keep reading to learn the key benefits and challenges industries face and how a solution like a drive-in rack can drive the future of warehouse management.
The Rise of Warehouse Automation
Warehouse automation is no longer a futuristic concept – it’s a necessity for companies aiming to keep up with growing consumer demand and the complexities of global supply chains. The adoption of automated systems such as robotics, AI-driven software, and advanced material handling equipment has accelerated in recent years.
With warehouse utilization on the rise, these systems can help streamline processes, reduce human error, and optimize space, which is often a top concern for warehouse managers.
Automation can take different forms in a warehouse setting. While robots and conveyors might be the most visible elements, storage systems also play a vital role in enhancing warehouse efficiency. Companies today need to store more products in less space, and innovations in storage systems like drive-in racks provide a powerful solution to this challenge.
What Is a Drive-In Rack?
A drive-in rack is a type of high-density storage system that allows forklifts to drive directly into the storage lane. Unlike traditional racking systems, where aisles are necessary for forklift access, drive-in racks eliminate these aisles by providing deep storage lanes. This results in a more efficient use of warehouse space.
Drive-in racks work best for businesses that handle large quantities of similar items – especially those following the Last-In-First-Out (LIFO) method of inventory management. Pallets are loaded and retrieved from the same entry point, which helps maximize storage density.
This is particularly useful for industries like food and beverage, retail, and manufacturing, where product lines often consist of bulk goods or homogeneous items.
Key Benefits of Drive-In Racks in Warehouse Automation
Before taking the leap into warehouse automation solutions like drive-in racks, it pays to know about the advantages to doing so. Companies will be better positioned to maximize benefits and understand the impact on their business plans.
1. Maximization of Storage Space
One of the most significant benefits of drive-in racks is their ability to maximize storage space. By eliminating the need for multiple aisles, businesses can store more pallets in the same footprint compared to traditional selective racks. This is a game-changer for warehouses with limited space or those looking to avoid the costs of expansion.
For industries handling seasonal products, drive-in racks offer a flexible solution, allowing them to efficiently store large volumes of inventory during peak seasons and scale down when needed.
2. Improved Inventory Control
While drive-in racks follow the LIFO principle, advancements in automation have enhanced how companies manage their inventory in such systems. Automated storage and retrieval systems (AS/RS) and warehouse management software (WMS) can now be integrated with drive-in racks to track inventory in real-time.
For industries with lean margins, this reduces the risk of misplaced products. It also provides managers with better oversight into stock levels, ensuring more efficient order fulfillment.
3. Enhanced Labor Productivity
Automation aims to reduce human intervention in routine tasks, and that means workers gain more time to invest in complex tasks. Drive-in racks can help achieve this goal by minimizing the time spent by workers navigating through aisles.
Along with the help of forklifts and automated systems, workers can retrieve or store pallets more quickly, reducing overall operational costs and improving warehouse optimization.
Additionally, integrating drive-in racks with automated guided vehicles (AGVs) or autonomous mobile robots (AMRs) can help as part of a smart warehouse, as well. These advances further reduce the need for manual labor in retrieving pallets. This allows businesses to operate 24/7, increasing responsiveness to customer demands.
4. Cost Savings
By trimming space and labor needs, drive-in racks contribute to significant cost savings, too. Since fewer aisles are required, for example, companies can reduce costs related to lighting, heating, and cooling large areas that are no longer needed.
Businesses that use drive-in racks also benefit from lower capital expenses compared to fully automated, high-tech storage systems. This makes drive-in racks a more affordable option for companies that may not be able to invest in fully robotic warehouses.
Challenges Faced in Modern Storage Solutions
The benefits of automation and drive-in racks are substantial. Even so, industries face several challenges when adopting these systems. Understanding these challenges is crucial for businesses looking to make the most of modern storage solutions.
1. Complexity of Implementation
Integrating drive-in racks and other automated storage systems requires a thoughtful approach to warehouse design and layout. Existing infrastructure may not always support the weight and space requirements of these systems.
Additionally, businesses need to ensure that their inventory management software is compatible with the automated systems they choose to implement.
2. Maintenance and Durability
Drive-in racks, like any other physical structure, are subject to wear and tear. Forklifts driving in and out of the racks can lead to potential damage over time, especially in high-traffic warehouses. Regular maintenance is crucial to avoid costly repairs or the risk of a collapse, which could endanger workers and inventory.
3. Inventory Constraints
Drive-in racks work best for warehouses with large quantities of similar items, as they follow the LIFO system. For companies that handle a diverse range of products or require a First-In-First-Out (FIFO) approach, drive-in racks may not be the most efficient solution. In such cases, other storage systems, like push-back or flow racks, may offer a better alternative.
4. Initial Capital Investment
Although drive-in racks are more affordable than fully automated systems, they still require a significant initial investment, especially for businesses that need to redesign their warehouses to accommodate them. Companies must carefully weigh the long-term benefits against the upfront costs before committing to such a solution.
The Future of Warehouse Automation
The future of warehouse automation lies in the seamless integration of storage systems with advanced technologies like robotics, AI, and machine learning. Drive-in racks, when paired with intelligent automation, will continue to play a crucial role in helping businesses optimize their storage strategies.
As industries grow more reliant on real-time data and predictive analytics, storage systems will evolve to meet these demands. Automated drive-in racks, equipped with sensors and smart monitoring systems, could become the norm. As a result, businesses will gain the agility needed to stay competitive in an increasingly dynamic marketplace.
What’s Next for Storage Solutions
Warehouse automation is transforming the logistics landscape, and drive-in racks are an essential part of this evolution. By maximizing storage space, improving labor productivity, and offering cost-effective solutions, these systems help businesses stay competitive while navigating the complexities of modern supply chains.
While challenges exist, the future of storage automation promises even greater advancements, as industries continue to embrace cutting-edge technologies that enhance efficiency and performance.
For those looking to upgrade their warehouse systems, choosing a drive-in rack offers a solid foundation for building a more efficient and automated future.