Science & Environment
NTU Scientists Build New Ultrasound Device Using 3D Printing Technology
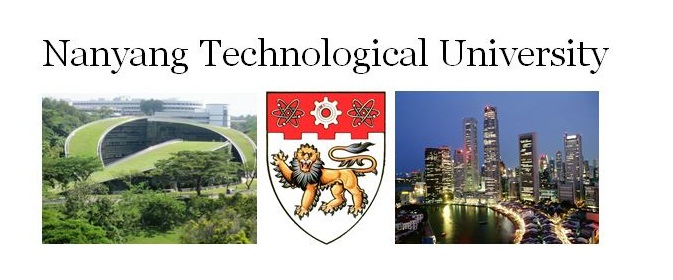
With clearer images, doctors and surgeons can have greater control and precision when performing non-invasive diagnostic procedures and medical surgeries.
The new device will allow for more accurate medical procedures that involve the use of ultrasound to kill tumours, loosen blood clots and deliver drugs into targeted cells.
This innovative ultrasound device is equipped with superior resin lenses that have been 3D printed.
In current ultrasound machines, the lens which focuses the ultrasound waves are limited to cylindrical or spherical shapes, restricting the clarity of the imaging.
With 3D printing, complex lens shapes can be made which results in sharper images. The 3D printed lenses allow ultrasound waves to be focussed at multiple sites or shape the focus specially to a target, which current ultrasound machines are unable to do.
Industry partners keen to develop commercial applications
The novel ultrasound device was developed by a multidisciplinary team of scientists, led by Associate Professor Claus-Dieter Ohl from NTU’s School of Physical and Mathematical Sciences.
The ultrasound device had undergone rigorous testing and the findings have been published in Applied Physics Letters, a peer-reviewed journal by a leading global scientific institute – the American Institute of Physics.
With this breakthrough, the NTU team is now in talks with various industry and healthcare partners who are looking at developing prototypes for medical and research applications.
Associate Professor Claus-Dieter Ohl said, “In most medical surgeries, precision and non-invasive diagnosis methods are crucial. This novel device not only determines the focus of the wave but also its shape, granting greater accuracy and control to medical practitioners.”
Overcoming current limitations
Ultrasound waves are produced by firing sound waves at a glass surface or ‘lens’ to create high-frequency vibrations.
In conventional ultrasound machines, the resulting heat causes the lens to expand rapidly, generating high frequency vibrations that produce ultrasound waves.
With lenses that are 3D printed, the new ultrasound device overcomes the limitations of glass. Customised and complex 3D printed lenses can be made for different targets which not only results in better imaging, but are cheaper and easier to produce.
“3D printing reinvents the manufacturing process, enabling the creation of unique and complex devices. In turn, the way medical devices are created needs to be rethought. This is an exciting discovery for the scientific community as it opens new doors for research and medical surgery,” said Assoc Prof Ohl.
This breakthrough taps into an ultrasound market which is expected to grow to about US$ 6.9 billion by 2020. It is also expected to promote new medical techniques and research opportunities in health sciences such as surgery, and biotechnology.
For example, researchers could use the sound waves to measure elastic properties of cells in a petri dish, seeing how they respond to forces. This will be useful for example, to distinguish between harmful and benign tumour cells.
“This is a very promising breakthrough, potentially offering significant clinical benefits including to the field of cancer imaging. This technology has the potential to reduce image distortions and more accurately differentiate cancerous from non-cancerous soft tissue,” said Adjunct Assistant Professor Tan Cher Heng, LKCMedicine Lead for Anatomy & Radiology and Senior Consultant with the Department of Diagnostic Radiology at Tan Tock Seng Hospital.
About Nanyang Technological University, Singapore
A research-intensive public university, Nanyang Technological University, Singapore (NTU Singapore) has 33,500 undergraduate and postgraduate students in the colleges of Engineering, Business, Science, Humanities, Arts, & Social Sciences, and its Interdisciplinary Graduate School. It has a new medical school, the Lee Kong Chian School of Medicine, set up jointly with Imperial College London.