Technology
Boring vs Drilling: What Are the Differences?
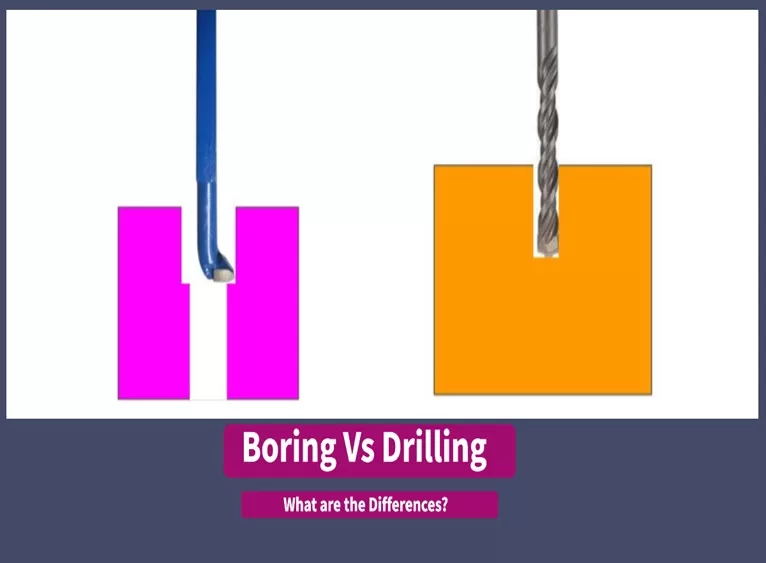
Holes are critical features in CNC machining that are used for specific functionality or assembly purposes. Typically, they are created with CNC drilling, which involves removing the material by a rotating drill bit. Meanwhile, boring is used to enlarge the drill holes with desired specifications, surface finish, and tolerances. Regardless of the difference between drilling and boring, together they offer an accurate practice in engineering hole creation.
Furthermore, this article will discuss boring vs drilling in detail, their processes, tooling, advantages, and disadvantages.
What is Drilling?
Drilling is a machining process that creates circular holes(through and blind) in workpieces using a rotating drill bit. A drill bit attached to the machine’s spindle digs the material as it starts to rotate inward from the workpiece surface. Meanwhile, the helical structure of the drill bit facilitates the material evacuation as drilling advances to work thickness.
You can hand drills, power drills, and CNC machines to drill the holes in a variety of materials, wood, plastics, composites, and soft metals. However, it is challenging to drill hard materials like tool steel, cobalt, and tungsten alloys.
Typically, CNC drilling is preferred over other methods due to tight tolerance capability and fast speeds. A CNC drilling program(G & M codes) dictates the spindle movement to achieve desired hole specifications.
Advantages of CNC Drilling
- CNC drilling creates new holes, slots, and cavities in the workpieces
- The speed of machining is faster than conventional drilling or hole-making processes like hand drills and manual lathes.
- You can CNC drill both shallow and deep holes effectively with minimal tool wear.
- It is cost-effective for simple and accurate hole drilling.
Disadvantages of CNC Drilling
- The drilled hole surface often contains microchips, burrs, and other irregularities attached to it, so post-processing like reaming or other operations might require to smooth the surface.
- Drilling is limited to simple and cylindrical-shaped holes
- Deep and micro-hole drilling is challenging with CNC drills as they have tooling limitations.
What is Boring?
Boring is the process of enlarging and refining the drilled holes with boring bars & inserts. Manufacturers use boring operations to achieve the desired diameter, surface finish, and precision of an existing hole on workpieces.
There are different types of boring bars, line boring back boring, horizontal boring, vertical boring, etc. Meanwhile, CNC mills, lathes, drilling machines, or specialized boring machines are used for this.
Advantages of CNC Boring
- The boring refines the pre-drilled holes to the desired dimensional accuracy and surface finish.
- A boring bar or insert enlarges the hole diameter smoothly especially where tight tolerances are not necessary for functionality & performance.
- Boring can be used for through, blind, threaded, and other hole types.
Disadvantages of CNC Boring
- It is more complex in terms of tooling setup and operation handling.
- You can not create new holes with a boring process, it only works with already existing holes.
Key Difference Between Drilling and Boring
Let’s elaborate head-to-head comparison of boring vs drilling on different criteria; tooling, precision, processes, and work material options.
Tooling
CNC Drilling uses high-speed steel (HSS), carbide, and hardened steel tools, often coated with tougher materials like titanium nitrides. The bit size can vary from 1/64 to 11/2 inches ( standard drills in fraction inches). Consequently, there are several types of drill bits, including step drill, countersink twist, spiral, auger, and plug bits.
On the other hand, the boring process uses boring bars (also called inserts) to refine the drilled hole and meet the desired dimensions and surface finish quality. The boring bars rely on a single cutting edge or insert located at the tip of the bar aligned to control the depth and diameter of the bore.
Chip Formation & Evacuation
In drilling the hip evacuation can be in a downward or upward direction based on the type of hole you are drilling ( blind or through) and the geometry of the drilling tool. For example, a twist bit forms chips and removes them in an upward direction.
In Boring, material removal is not an issue. It removes minor material (then chips will be formed) and even continuous feeding does not affect the tool’s integrity.
Tolerance of Holes
In bore vs drill, the boring process is more precise and accurate due to tight control over depth and diameter. An advanced CNC drilling machine can achieve a tolerance as low as ± 0.0025mm. On the other hand, boring can activate more tightly than this based on a particular bore or insert.
Material Compatibility
The boring operations have more material options in comparison to boring vs drilling, you can not drill tough materials like titanium alloys, hardened steel, etc. On the other hand, if there is a pre-drilled, casting, or any other type of hole on these hard materials, boring can refine them up to specifications.
Summary Table for Boring Vs Drilling
Criteria | CNC Drilling | CNC Boring |
Tooling | Uses a variety of drill bits made with HSS, carbide, etc. | Boring bars (and inserts) with single-cutting edges |
Precision | Moderate precision; tolerances around ±0.0025 mm. | Higher precision for refining hole depth and diameter. |
Chip Formation | Chips evacuated based on tool and hole type. | Minimal chip formation; continuous feeding without tool damage. |
Material | Limited with tough metals. | It refines pre-drilled holes on hard materials also. |
Application Scope | Effective for producing standard, high-volume holes. | It is suitable for high-precision work. |