Brand Strategy
5 Simple Ways to Improve Warehouse Handling Efficiency Today
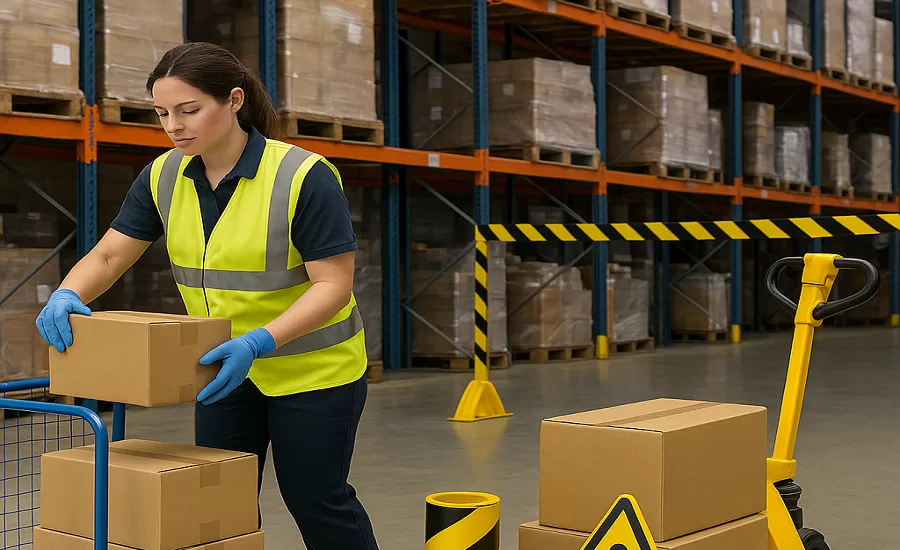
Inefficient warehouse handling is what’s silently draining profits. Studies suggest poor handling practices can inflate operational costs by 10-20% through wasted labor and damaged goods, often being deceptively damaging.
Every time an item is moved or stored inefficiently, time and money are lost. These bottlenecks ripple outwards and can impact customer satisfaction, because costs and delays are past on. This article looks at five ways any warehouse manager can work to improve workplace efficiency and strengthen supply chain resilience. Optimize your layout and slotting strategy
Excessive travel time is a major efficiency killer. Even in a small coffee shop, each time a worker crosses one another’s path, it’s deemed an inefficiency. So on the scale of a warehouse, produce and people movement is important.
It’s often called an ABC analysis. Position your fastest-moving A items in the most accessible locations, closest to packing and shipping zones. Slower B and C items can then occupy less prime real estate. It’s important to keep aisles wide enough for both equipment and personnel to pass safely without congestion.
Use durable floor markings to clearly define traffic lanes, as this will reduce accidents and frictions. You can learn more about this while investing in staging areas and storage zones to reduce confusion. Then, a clear warehouse identification system ought to be implemented, as this means large legible signs for aisles, rack levels and individual bin locations. Using barcodes is ideal but even simple alphanumeric location names can drastically cut search times and errors. Staff shouldn’t waste minutes hunting for inventory, so proper identification is what will prevent this. And, if each identification is sped up by a few seconds, this scales dramatically when considering the number of workers.
Standardize workflows and processes
Inconsistency is what breeds inefficiency and errors. Develop simple and clear Standard Operating Procedures for all of the core handling tasks. You can document the best practices for receiving putaway picking methods (like zone batch or wave) as well as packing and loading. Don’t just file these SOPs away of course, use visual aids like charts or photos posted in relevant work areas to reinforce the correct procedures.
Conduct brief but regular training sessions (better than long, infrequent sessions) that focus not just on the how, but the why behind each step. Deepening understanding is what can help these ideas stick. Standardized processes also make training new hires much faster and reduce variability in the output. This then improves overall workplace efficiency across the board allowing for easier performance tracking.
Enhance dock operations for smoother flow
Shipping and receiving docks are the nerve centers, and bottlenecks here paralyze the entire warehouse. You can start by proactively scheduling truck arrivals and departures, focusing on clear time windows to carriers as this will help prevent dock congestion. Designate ample clear staging space near the docks for both incoming goods and outgoing shipments. This prevents clutter and keeps the respective pathways open.
You should also looking to the loading bay equipment. Functional dock levelers can help bridge the gap safely and efficiently between trailer beds and the dock floor, while dock seals or shelters protect goods and the warehouse environment from the elements.
Equip your team with the right handling aids
Using the wrong tools or poorly maintained ones will, of course, directly hinder handling speed and safety. So, there needs to be an adequate supply of appropriate material handling equipment. This includes well-maintained pallet jacks, hand trucks, carts and dollies all intentionally suited to your products and layout.
Ergonomic designs shouldn’t be overlooked as these will reduce strain and improve the consistency of employee performance over the entire work day. Packing stations can also be optimized for maximum throughput, as they should be consistently stocked with the necessary supplies, like quality packing tapes & tools. So, frequent checks of these supplies are needed.
Sharp safety cutters, ergonomic tape dispensers and so on should be readily available. Don’t overlook basic maintenance either, as having functional workshop equipment like workbenches and basic hand tools allows for quick in-house repairs. So, you don’t always need to call someone in. Fixing a wobbly cart wheel or replacing a dull cutter blade immediately helps prevent bigger delays (and potential injuries) later down the line.
Start improving today
Boosting warehouse handling efficiency doesn’t actually require a massive overhaul or large machinery investment. With what you already have, you can simply focus on optimizing the layout through clear warehouse identification, as well as standardize key processes and ensure there are always the right handling tools nearby.
These steps will help reduce wasted movement and minimize errors. Of course, you want to gather as much data as possible on these inefficiencies so you can identify them. But, at some point, they’re so minute that they cannot be recorded without introducing a new layer of inefficiencies. So, the path forward is to implement tried-and-tested methodologies that have a low initial investment, and rely on worker feedback and broader KPIs to judge the results.